Eddy Current Separators (ECS), also known as non-ferrous separators, consist of a conveyor belt system with a rapidly rotating magnetic rotor at the end that generates an induction field, creating a rapidly changing magnetic field. An animation can be seen here: //youtu.be/-b0nwPgWh8Q
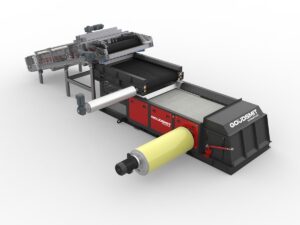
Separation
The separation is based on the principle that every electrically conductive particle located in an alternating magnetic field temporarily becomes magnetic. Simply put, for a brief moment, all non-ferrous metals that pass the magnetic rotor become magnetized, causing them to be propelled away due to the alternating magnetic field. This results in non-ferrous metals such as aluminium, copper and brass, to be pushed away from the natural ballistic trajectory path.
Mono-Layer and Material Feed
For the best separation results and highest yields, a mono-layer is required. This is particularly important for the ‘fines fraction’ (particle size 0-10 mm). By utilizing the full belt width of the machine, the capacity (throughput) achievable is maximised.
The difficulty in creating a mono-layer for product streams, such as IBA (incinerator bottom ash) and RDF (refuse-derived fuel), is due to the moisture content and stickiness, for example the cement-like mass in IBA which sticks to the surface of vibratory feeder.
This prevents the vibratory feeder from distributing the product evenly over the full belt width of the ECS, as the product follows the path of least resistance. This means that regular cleaning of the vibratory feeder is required, resulting in down-time and increased maintenance.
To avoid the use of a vibratory feeder, Goudsmit developed a proven solution by replacing the vibratory feeder with a “feeder module”, consisting of two conveyors and product spreaders.
The first conveyor is at an angle and feeds the material up to the product spreaders. These product spreaders (also called ‘churners’), spin the material so that it distributes evenly over the full belt width. If the amount of material fed to the product spreaders exceeds the capacity, the excess material slides back down.
The second conveyor (magnetic separator) transports the material horizontally towards the magnetic head pulley, fitted at the end of the conveyor belt. The strength of the magnetic head pulley (Gauss strength) depends on the application.
- For ferrous particles of 1mm to 100mm – 1800 Gauss.
- For ferrous particles of 0.5mm to 100mm – 3000 Gauss.
- For ferrous and stainless-steel particles of 0.5mm to 100mm – 6000 Gauss.
- For ferrous and stainless-steel particles of 0.1mm to 30mm – 9000 Gauss.
By using the correct magnetic head pulley for the application, ECS separation and recovery of magnetic fractions are significantly improved.
Once the magnetic fractions are removed, the material drops onto the ECS in a mono-layer, perfectly spread across the entire width of the belt and free from fluctuations in density.
As the ferrous metals are removed, there is no interference from ferrous at the ECS separation step, thus improving the non-ferrous recovery.
The Goudsmit ECS design for IBA is a complete machine with optimal ferrous and non-ferrous recovery without time-consuming cleaning and maintenance requirements.
Magnet Rotor
The Goudsmit magnet rotor has 38 high intensity poles (38HI) with a magnetic strength of 3500 gauss at the belt*. A high magnetic force is required for the heavy non-ferrous metals, such as copper and brass. The ability to recover non-ferrous depends on the magnetic strength of the poles, number of poles and rotor rotation speed.
*flux density at 3 mm thickness on the belt with a tolerance of ±10%
Flux Density
The Goudsmit EddyFines focuses on the most difficult non-ferrous parts to recover, parts of 0-10mm, and non-ferrous metals that are relatively heavy, so-called heavy non-ferrous (HNF), such as copper, gold, silver, and palladium.
The EddyFines distinguishes itself by the extra-large 38HI magnet roller, currently the largest on the market. This type of rotor is extremely powerful, capable of ‘ejecting’ the smallest particles of ≥ 0.3mm across.
The large rotor allows Goudsmit to fit more magnetic pole pairs and magnet volume, resulting in pure separation of tiny non-ferrous particles.
Because the EddyFines targets smaller NF particles, it is often located at the end of a machine or production line.
The EddyFines often used as part of an eddy current cascade. For the middle fraction, a 22HI EddyXpert (22 high intensity pole ECS) can be used, followed by the EddyFines separator for the recovery of the fine non-ferrous fraction.
These configurations provide a significantly higher separation yield.
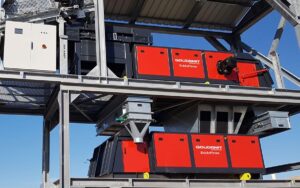
The EddyXpert you can be configured with two different Eddy Current rotors:
1) 12 pole. This magnetic rotor has a deep, powerful magnetic field and relatively few pole changes. The 12 pole is used for coarse materials, 20-300 mm. Due to its deep field, this is the perfect pre-separator.
2) 22HI pole. This magnetic rotor has a shallower field than the 12 pole, but it has a higher magnetic force and more pole changes close to the belt surface. This makes the 22HI suitable for material flows with a fraction of 5-60mm.
HI (High Intensity)
The Goudsmit Eddy Current magnet rotors, such as the 22HI and 38HI, feature a HI-magnet configuration. This is a Goudsmit exclusive which generates extremely high magnetic forces.
The HI magnetic rotors are therefore also suitable for small fractions that are difficult to process and weakly magnetic non-ferrous particles that are difficult to separate.
Separation Plate / Splitter
For the final, definitive separation of the two product streams, the Goudsmit ECS design has a separation plate between the inert and non-ferrous stream.
The parts of the separation plate that are in contact with the material are executed in manganese steel. This material is self-hardening for a long service life, perfectly suited for IBA streams.
The separation plate in the EddyFines has a sharp tip at the top of the splitter plate, allowing the splitter to “cut” into the material stream.
The splitter plate can be moved up and down, backwards, and forwards with fine adjustments, resulting in maximum non-ferrous recovery.