We want to avoid any machinery downtime and production losses and ensure maximised yields for your organisation. Serving customers is a fundamental aspect of our efficacy and makes business sense. This also applies to project engineering advise and installation of all turnkey solutions for a subsequent guarantee of a smoothly running plant.
We offer an exclusive after-sales service, providing our customers with qualified assistance always. Our team of fully trained and experienced engineers and technicians remain at your disposal.
On-site Service Visits
Regular check-ups are strongly advised to avoid down-time and reassure trust in your equipment. All our specialised, fully-trained technicians can undertake scheduled on-site maintenance visits to suit your needs.
Benefits of regular servicing:
- Regular replacement of wearing parts ensure long lifespan of our products and avoid unnecessary production downtime.
- Optimisation of equipment and plant performance.
- Maximise profit by minimising downtime.
- Reducing energy consumption and impact on the environment.
- Education and training of staff members.
- Consultation of skilled service engineers with in-depth hands-on experience.
Before a client or customer audit or prior to a peak-production phase, a service visit can really boost confidence and give peace of mind. Regular check-ups also increase the units’ lifespan while reducing service costs to a minimum through scheduled service visits and break-down prevention.
This also means customers facing challenges without any hands-on, inhouse support can rely on us to support and assist them promptly.
Spare Parts
It is standard practice for all equipment we install to have the highest quality components and a lot of these are kept in stock at our partner’s premises for ease of access.
It allows us the ability to offer day-to-day dispatch of an extensive range of spare parts that all meet strict requirements in terms of quality and documentation.
Equipment and Spare Parts Traceability
Every single piece of our partner’s equipment is applied with a serial number. This way, our system ensures that we are always able to track and assist with support.
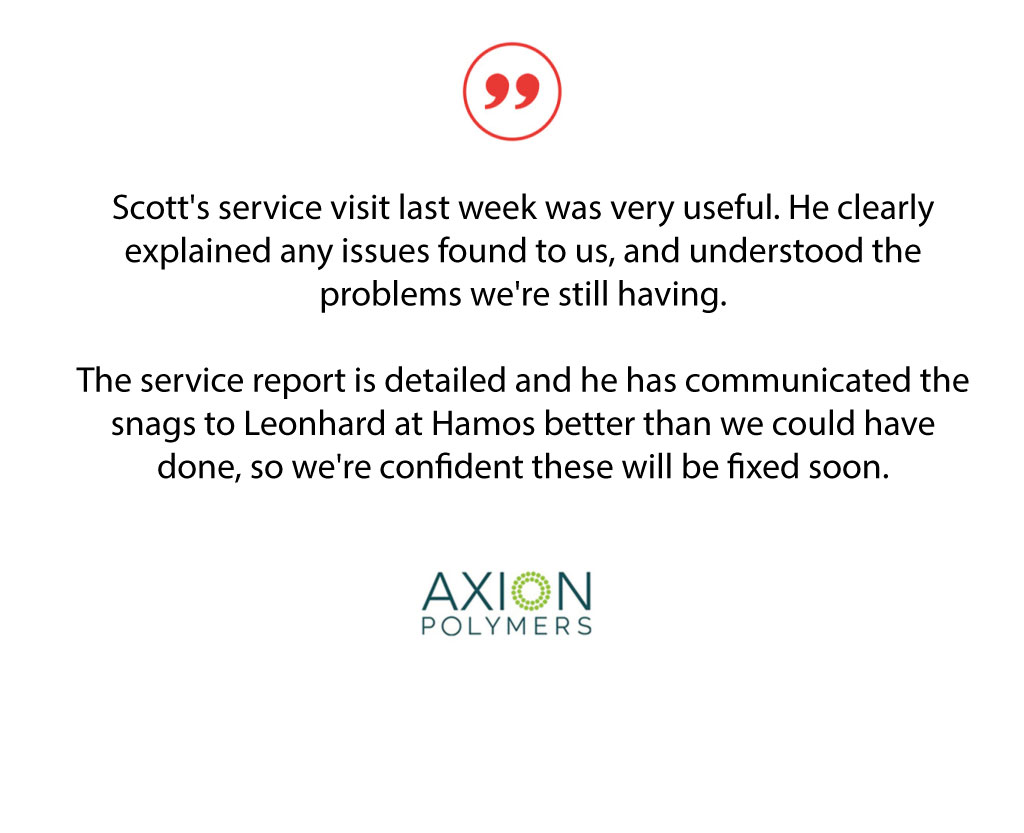
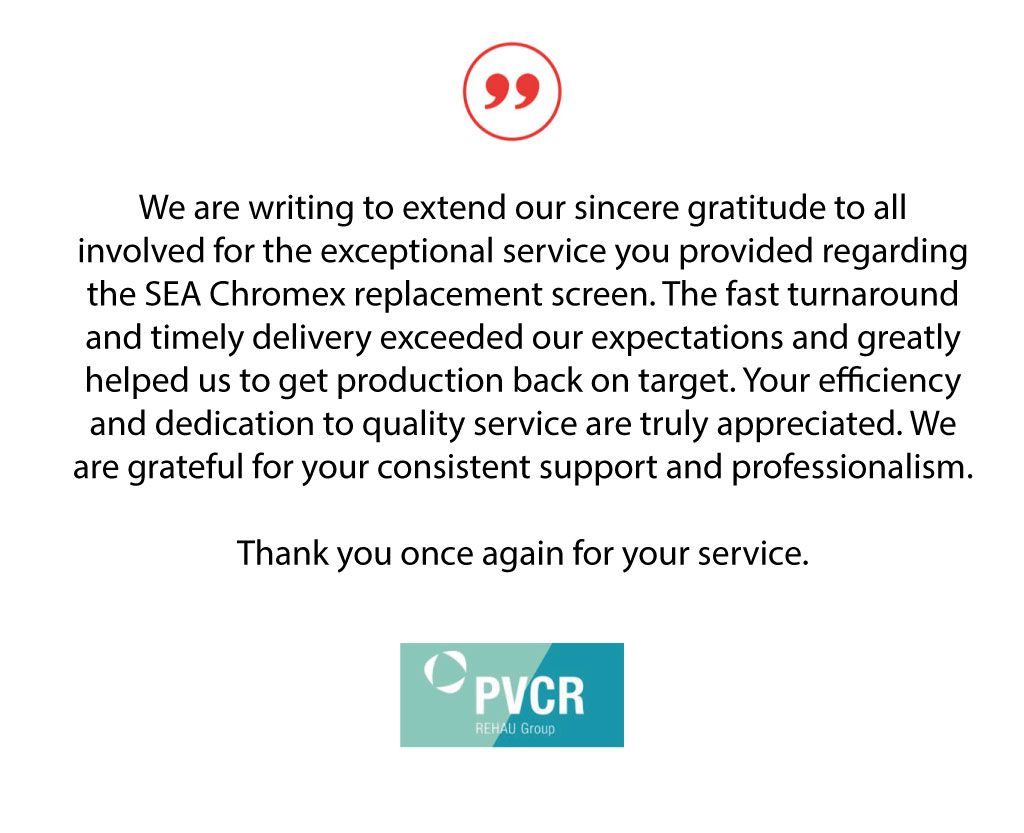
Machinery & Metal Detector Breakdowns
If the worst case happens, be assured we are here to help.
It makes no difference to us if you already have a service contract with another service provider or if you didn’t purchase your unit from us directly. Our promise is to help you resolve the issue promptly to get you up and running again as quickly as possible.
Our Service Department will help diagnose your issues either over the phone or in person with a scheduled service visit.
Remote Access Assistance
Our Cimbria SEA machinery can be accessed remotely (modem in place dependent). When needed, an operator can request an interactive control of the sorter through an internet connection. We can control, modify and memorize the program data, through a specific server.
Commissioning & Personnel Training
We can perform training for all equipment supplied at our customer’s premises, providing a complete and detailed explanation on machine functionality. The customer’s operator in charge will be duly trained during the machine start-up phase by one of our experienced technical engineers. Full training can also be provided for any new employees.
Product Trials
We can facilitate trials if required to understand what can be sorted and separated from your product stream.
To contact us for machine spare parts, servicing or repairs you can either call us on 01223 223900 and speak to Lizzie or email her on service@allcontrols.co.uk